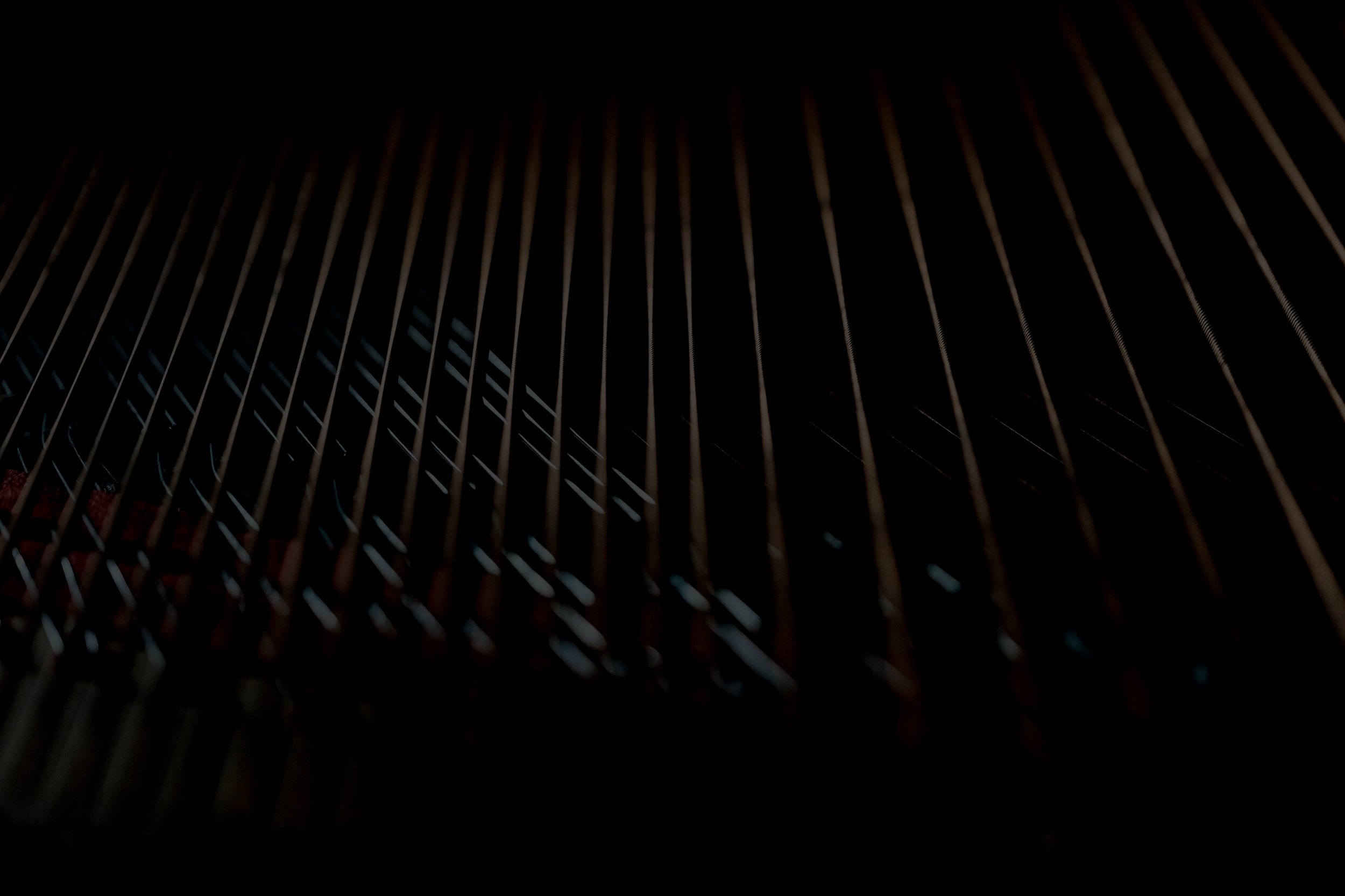
PRODUCTS
PlasmaANNEALER
PlasmaANNEALER is a continuous heat treatment machine for ferrous and non-ferrous wire, rod, tube, rope and strip.
Why choose PlasmaANNEALER?
Branched utility
Plasma heat treatment can be used for annealing, stress relieving or hardening applications.
Materials
Copper and copper alloys
Stainless steel and steel alloys
Nickel, nickel alloys and nitinol
Titanium and titanium alloys
Aluminium and aluminium alloys
Molybdenum and tantalum
Gold, silver and other precious metals
Watch a video of PlasmaANNEALER
Benefits
Bright surfaced finish, scratch-free and without spark damage
Simultaneous degreasing and deoxidation in inert atmosphere
Adjustable mechanical properties
Fine and uniform grain size
Homogeneous grain in transversal and longitudinal direction
Less die wear in fewer wire breaks in subsequent drawing
High output annealing
Lowest production cost in class
Low energy, gas and maintenance costs
Small production footprint
Small power connection required
No warming-up/cooling-down time
Computer based controls with production and quality control features
What else?
Heat treatment: annealing, stress relieving, hardening
Material form: wire, rod, tube, strip, shaped wire, strand, rope
Process type: continuous
PlasmaPREPLATE
PlasmaPREPLATE process was designed for surface cleaning, surface oxide removal and annealing prior to plating for wires, strip or tube.
Why choose PlasmaPREPLATE?
PlasmaPREPLATE is a chemical-free alternative to chemical cleaning and fluxing. PlasmaPREPLATE can be installed in-line with electroplating or hot dip plating.
Materials
Copper and copper alloys
Steel alloys
Nickel, nickel alloys and nitinol
Aluminium and aluminium alloys
Watch a video of PlasmaPREPLATE
Benefits
Heat treatment - homogenous mechanical properties
Surface cleaning - removal of fine surface deposits
Degreasing - removal of wet lubricant for dry surface finish
Surface oxide removal - deoxidation under ion bombardment
Surface activation - surface preparation for better coating adhesion
Horizontal PlasmaPREPLATE for electroplating:
High-speed surface preparation
Simultaneous heat treatment
No acid pre-cleaning, no rinsing
Improved plating performance
Reduced cost of electroplating
Vertical PlasmaPREPLATE for hot-dip plating:
High plating speed
Acid-free surface preparation
Flux-free hot dip plating
Strong intermetallic layer
Low cost of operation
Integrated surface quality control
What else?
Material form: wire, rod, tube, strip, flat wire
Process type: Continuous
PlasmaSUPREX
PlasmaSUPREX is a plasma treatment machine designed for general surface preparation, preheating and annealing prior to any coating process including extrusion.
Why choose PlasmaSUPREX?
PlasmaSUPREX (SUrface PREparation for EXtrusion) offers the most cost effective and environmentally friendly technology, available on the market, with simpler production and higher end product quality.
This product family is a further development of PlasmaPREPLATE. It is a more specialized product for the extrusion market, launched in 2014 for plasma surface preparation before extrusion.
Materials
PEEK, PEAK, PTFE, PFS, PA, etc.
Benefits
Low processing / production costs
Drastic reduction in energy consumption
Nearly no water consumption
No chemicals required (no toxic waste or slag produced)
Higher flexibility on PEEK material options
More process steps in one machine
Better thermomechanical and thermoelectrical properties of the product
What else?
Material form: wire, rod, tube, strip, flat wire
Process type: Continuous
PV Ribbon Line
PV Ribbon Line is used for production of PV Ribbon. The production includes annealing and cleaning of copper ribbon prior to hot-dip tinning and spooling.
Why choose PV Ribbon Line?
This is an acid-free, flux-free, environmentally friendly process. It provides the operator with safe and clean working conditions. The production is fully automated utilizing an easy-to-use operator interface with integrated quality control features.
PV Ribbon Line components:
Payoff or integrated with rolling mill
Annealing and surface preparation
Tinning and wiping
Cooling
Takeup with accumulator
Operational benefits:
High production speed – up to 10m/min
Acid-free, flux-free and operator-friendly production
High production up time with utilization rate of up to 95%
Quick changeover between different product specifications
Short string-in time
Less scrap through better product control
Less tin waste due to flux-free production
Low power and gas consumption
Low maintenance costs
Computer process controls with user-friendly operator interface
Product quality benefits:
Smooth, consistent and shiny tin coat
Small tin coat thickness tolerance
Super-soft or extra-soft PV ribbon (Rp0.2% down to 50MPa)
Computer-based production know-how management
Computer-based quality control
Production recipe database
Integrated alarm system with fault record database
What else?
Process type: Continuous
Inlet Material: Rolled copper ribbon copper on 500kg spools
Size Range: Interconnect ribbon and bus bar
Finished Material: Tinned flat copper wire / PV ribbon on various spool sizes